Android app for batch - container traceability by production station
Traceability of transfers and assignments of batches to or from containers on the shop floor at your fingertips, made affordable by our professional Android application: the link between workstation, batch, bin, direction and time of execution
Parts are placed in or removed from bins at different times of the day (time stamping), at different workstations, or even if we distinguish between the entry and exit of a workstation: all this data can be used in csv (Excel) format to trace the passage of a batch or sub-batch or through our favorite no-code interface with your databases as option, and to identify, through upstream and downstream traceability, the customers impacted by a defect discovered retrospectively.
Our simple, mobile tool stores data on batch transfers, OFs (production orders), and barcode scans of OFs and bins/containers.
Over the past few years, regulatory requirements - notably for consumer safety and inventory management - have constantly demanded traceability of operations and products, as in the food, pharmaceutical and automotive industries, to name but a few.
In these cases, in addition to traceability of operations, traceability of materials and products is required, so that it is possible to track both a finished product throughout its production and the materials used in its production.
Before implementing traceability software: how do you prepare the traceability of OFs (production orders) by station?
Before installing this software for reconciling batches/OFs and bins, you need to bar-code, Qr-code and label the two main items for greater accuracy and speed. the two main things :
- batch or OF sheets: it’s easier to insert the item code in this field, alongside the batch code, to reduce data entry.
- bins or containers.
In both cases, we have productivity-friendly label printing solutions for warehouses and workshops to offer without major investment, ou des logiciels d’impression depuis postes fixes ou mobiles.
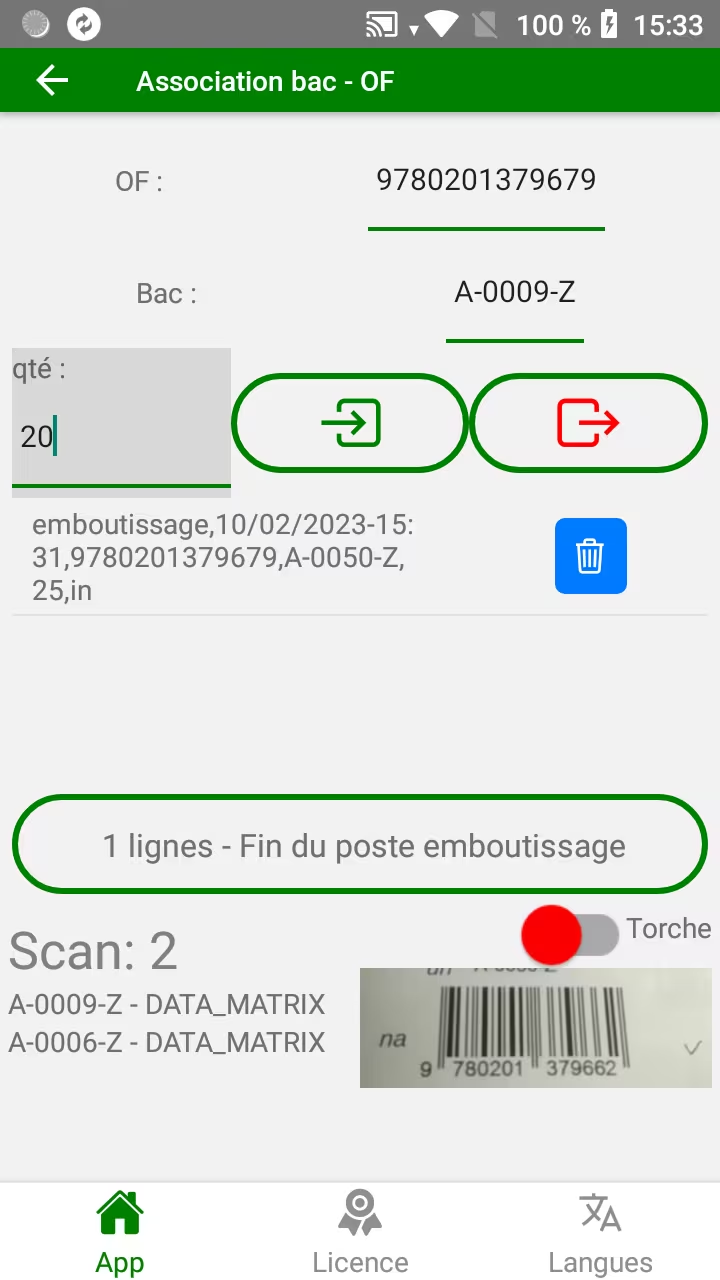
User interface for tracking batch-to-container and bin assignments
For use at all levels of the supply chain and production: from raw materials to finished products, in materials handling.
For workstations: create an Excel list of workstation codes to be traced: remember that a machine’s input and output workstations are 2 workstations. This can be done using the station table import option linked to this app (Android application).
Team acceptability
Making operators aware of their responsibilities: a computerized traceability project of this kind, including production monitoring, begins with the involvement of end-users, who will contribute to the data input to the system. The quality of the information entered throughout the process depends on the awareness and involvement of teams in the field.
The desire to track staff has been most prevalent in labor-intensive industries, with the more or less avowed aim of checking that operators are keeping to cadences and not allowing themselves hidden rest periods outside scheduled breaks, and perhaps even eliminating jobs. Make it clear that this is not the purpose of this application, even if any time-stamping allows it!
Time stamping allows you to put the steps back in order.
The advantage of the mobile tool in production:
Each station is not necessarily used throughout the day and throughout the process, so if you have fewer operators than the number of stations defined above, it’s more cost-effective to use one terminal per person rather than one terminal per station.
How do I use our mobile application?
Entering data into our applications is highly ergonomic, and requires no long explanations or manuals: the operator’s fingers and reflexes do most of the work, while the software avoids errors, inconsistencies and duplications, time-stamps entries in storage, and limits the number of buttons to be pressed.
At a selected workstation, once the OF has been scanned, the application switches automatically between scanning bin/container numbers, entering quantities by hand, and a button that defines the direction and end of cycle entry: quick and easy!
At the end or change of shift, a history is saved. This history can be exported to a uniquely named csv file or to a database through our favorite no-code interface with your databases as option, depending on the options.
Each record from several terminals, once collected in a single Excel table, is unique, enabling error-free processing of each one.
Option: import item table
The imported csv table of positions allows you to select positions with well-defined nomenclatures, and to create complete, comparable queries for analysis, or through our favorite no-code interface with your databases as option.
- Application in modules
- part of a range of modular automated supply-chain management applications for VSE warehouses
- other functions can complement this module: see common features .
- license required per terminal per year: users can try out 30 days of limited functionality,
Ask us for the test app loading link.
You already have an Android smartphone and would like to try out this mobile application module ?
Android app (Apk) provided on Productivix private repository, on request - link and loading QRcode provided To install it, read here
Quantitative test limit displayed according to modules, over 30 days. Qualification customer call before shipment.
Do you have a similar need? Don’t hesitate to tell us what you need: a copy of a pencil drawing of an interface, examples of interface files, a video of an obsolete software program in action will be enough.
Retail
Logistique,transports,SCM, production
Industries :